【連載コラム】倉庫業務マネジメント~つながる DX、WES の役割~第3章
- HOME>
- 【連載コラム】倉庫業務マネジメント~つながる DX、WES の役割~第3章
『倉庫業務総合研究会』の渡辺秀治氏による連載コラム、第3回は『オペレーションマネジメントの詳細機能」をお届けします。
<第1回・概要 はこちら>
<第2回・アクティビティの定義 はこちら>
【第3回】倉庫業務マネジメント~つながる DX、WES の役割~
第3章:オペレーションマネジメントの詳細機能
1) リソース管理
倉庫業務マネジメントは、リソースとして建物設備(トラックバースなど)、マテハン機器、保管設備、運搬機器、作業者、梱包等資材などが定義されています。
リソース管理では、こうしたリソースに関する性能データ、保全データ、物流標準原価データなどが管理対象となります。リソース管理では、こうしたリソースを管理するとともに、詳細スケジュールに従ってリソースの予約を行います。また、設備の段取りおよび状態管理や稼働履歴の管理も行います。
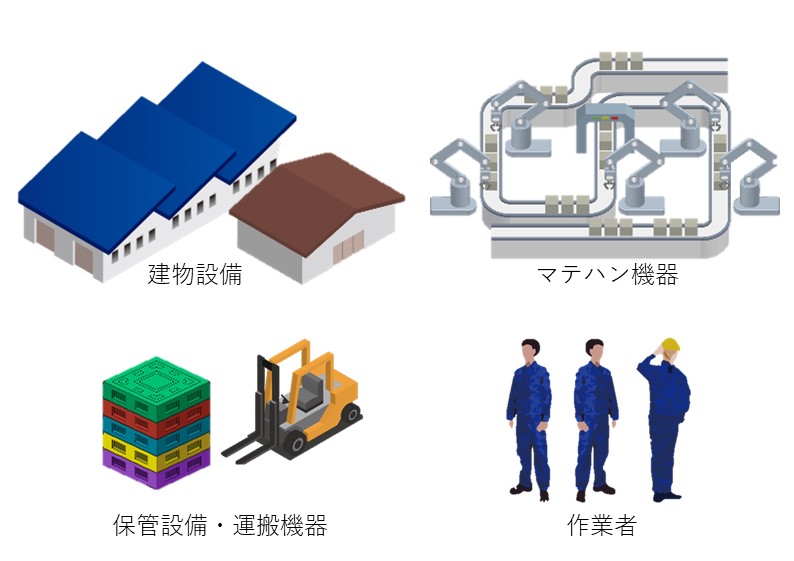
2)規定管理
規定管理は、装置や作業ごとに定義されている規格や書式および、実行の記録管理を行います。
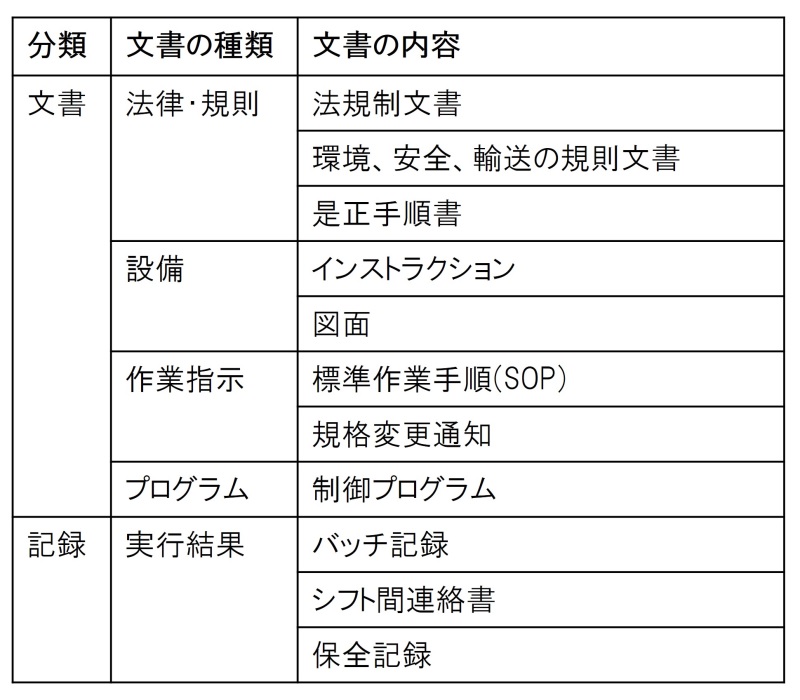
倉庫業務に関する、指示、実施の記録(仕分け指示書、入荷予定表、棚卸し管理表など)は、規定管理には含まれません。
3)詳細スケジューリング
詳細スケジューリングでは、それぞれの設備や貨物、荷役作業の特性に応じて優先度、属性、特性および、荷役ルールにもとづいて、作業の順序を決定します。品温帯、包装形態、積み荷順、荷下ろし順などさまざまな組み合わせ特性を考慮して適切な順序でスケジューリングすることで、段取りの最小化やスループットの最大化につながります。ここでは、資源の能力量が有限であることを前提として、負荷平準化やシフトパターンの調整を行い、代替作業や並行作業などを検討します。
① プランニングとスケジューリング
詳細スケジューリングはプランニングとスケジューリングを繰り返しシミュレーションし、作業実施のために最も効率的な予定を立案することです。
プランニングとは、目的達成のためのアクティビティ、および、下位のアクティビティを明確にし、必要な資源を確保する意思決定のことです。スケジューリングとは、制約条件を考慮し、アクティビティに対して、最適化が図られる、時間と空間と資源(リソース)を割り当てる意思決定を行います。
要求(主に受注)に対して、現実(荷役作業)は、常に変化し、流動的です。プランニングとスケジューリングは現実に追従して変化することが必要となります。
スケジューリングの結果、荷役作業の実現が不可能ならば、プランニングは、他の制約条件や制約条件の解除をスケジューリングに対して提示して、リスケジューリングを行わなければなりません。つまり、スケジューリングの実現可能性と効率性は、プランニングに対する一種の制約条件となります。
プランニングとスケジューリングの違いは、時間に対する視点の違いにも起因しています。プランニングは、一定の期間における目標数量(例えば、1日のピッキングす1万個)です。つまり、要求であり、受注の見込みです。一方、スケジューリングは作業の具体的なタイミングを表します。例えば、作業の開始・終了時刻、入荷時刻、出荷時刻などです。
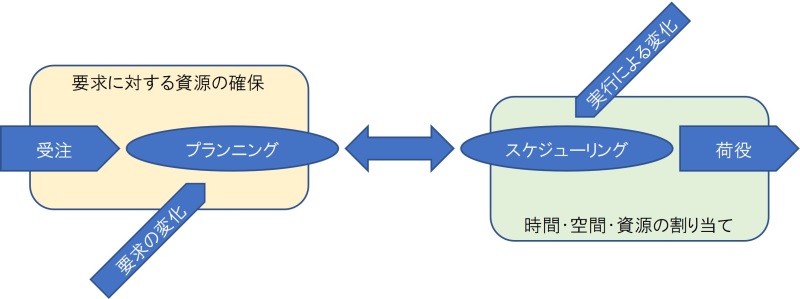
図 11:プランニングとスケジューリング
プランニングは、機能階層モデルのレベル4または、レベル3が実行し、組織全体または、拠点での最適化を実現するために実行することに対して、スケジューリングは機能階層モデルのレベル3が実行し、マテハン設備が効率的な稼働を実現するために実行されます。
② スケジューリングの制約についての定義
スケジューリングは、物流機能モデルのカテゴリの主に、荷役、包装、流通加工を対象として実行されます。それぞれのスケジューリング間では、相互の共通の資源や時間が競合する可能性があるため、それらの相互作用は明確に定義する必要があります。荷役作業を実行するために十分な必要な資源が確保できたことを確認して、スケジューリングを実行することになります。
荷役作業を実行するために必要な資源として、マテハン設備や作業者などの資源を確保することも重要です。マテハン設備や作業者の資格や職能については、リソース管理において正確な定義が必要となります。
<center>
荷役作業については、輸送の制約との調整も行う必要があります。詳細スケジューリングの結果として、作業のタイミングに合わせて、最適な輸送資源の手配および、トラックバースを配分することが重要です。また、着荷のスケジュール制約に合わせて、最適な荷役作業が行えるよう、設備のスケジューリングを行う必要があります。
設備保全においては、使用可能な設備や資源の能力を決定する一方で、保全計画にもとづき、マテハン設備の保全に必要な時間を確保する調整が必要となります。
生産管理などにおいて、品質検査が行われる場合は、出荷引き当てまたは、荷役済み貨物の一部が検査終了まで『待ち』のスケジューリングとしての制約が必要となり、検査作業の結果、不合格となったものに対する該当製品の『再引き当て』、荷役の『再スケジュール』も必要となる場合があります。同様に、入荷時に商品の受け入れ検査を倉庫業務マネジメントで実施する場合にお手は、入庫引き当てまたは、荷役作業において、『待ち』、『再引き当て』、『再スケジュール』が行われる場合があります。
③ マテハン設備・作業者能力の定義
エンタープライズモデルにおけるウェアハウス、ロケーションおよびそのロケーションに属するアクティビティに対して、マテハン設備および、作業者の能力情報を提供する機能を定義します。
能力情報は、現在、将来、あるいは過去において、マテハン設備および、荷役に携わる作業者資源への引き当て可能状態を表現しています。
過去の能力情報(能力量)は、使用済み能力量と未使用能力量に分類されています。現在および将来については、引き当て済み能力量、引き当て可能な能力量、引き当て対象外の能力量に分かれます。
能力量は引き当て済み能力量、引き当て可能な能力量、そして引き当て対象外の能力量の合計値となります。
引き当て済み能力量は、通常、スケジュールにもとづき、将来の作業に引き当てられた資源の利用予約になります。また、引き当て対象外の能力量とは、マテハン設備の状態、マテハン設備の使用状況(他の作業での使用状況を含む)、作業者の空き状況、その他の資源の引き当て可能状況など理由により、将来の作業に引き当てができない資源に対応します。そして、引き当て可能な能力量は、既に引き当て済みではなく、将来の追加作業に対して引き当て可能な資源となります。
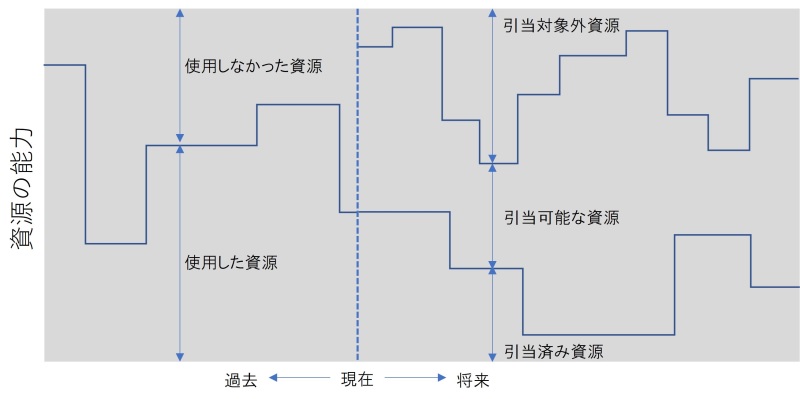
④ 在庫(保管量)についてのスケジューリング
倉庫業務マネジメントの荷役作業の制約において、在庫のマネジメントが最も重要な要素であることは言うまでもありません。
スケジューリングによって、在庫の推移を明確にし、出荷、引き当て、入荷を時間単位で明確にし、荷役作業が実現可能であることを検証したうえで、実行する必要があります。倉庫業務マネジメントにおけるスケジューリングは、前提として、荷待ちや欠品が発生していない状況下で行われます。しかしながら、出荷可能な商品が確保できているか、入荷した時点で保管スペースが確保できるか、 在庫の検証を行ったうえで詳細スケジューリングを実行しなければ指示通りの作業が実行できなくなります。(いずれも荷役作業のスケジューリングに対する制約となります。)
倉庫業務マネジメントでは、詳細スケジューリングでは、在庫量をスケジューリングし、輸送・配送業務、荷役業務および、保管スペースの最適化を行います。
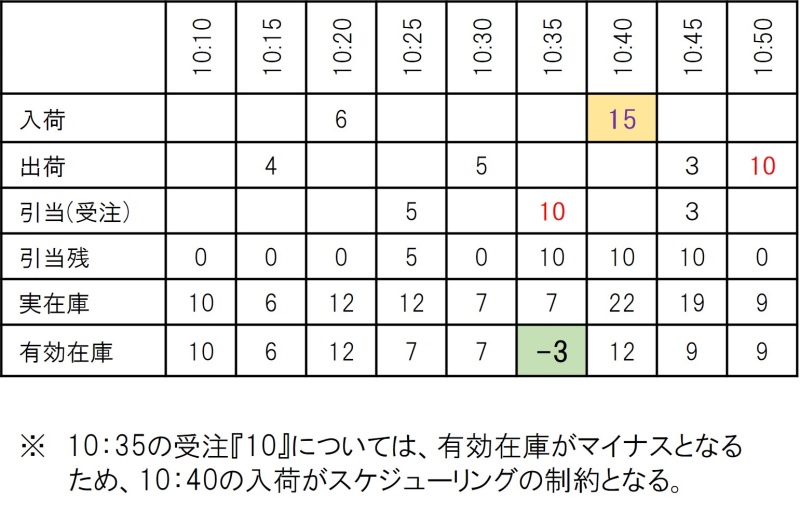
⑤ トラックバースの配分
働き方改革関連法によって、2024年4月1日から「自動車運転業務における時間外労働時間の上限規制」が適用されることに伴い、荷主企業が取り組むべき改善課題として、大きく次の2点が考えられます。
■配送ルートの最適化と積載効率の向上
■荷役(荷降ろし、積み荷)待機時間の短縮
倉庫業務マネジメントの荷役作業と連動した、トラックバースの資源配分については、重要な要素のひとつとしてあげられます。
また、トラックバースの最適な資源配分を行うことについては、設備の運用効率の向上を図ることになり、組織の資産運用効率が向上することにつながります。
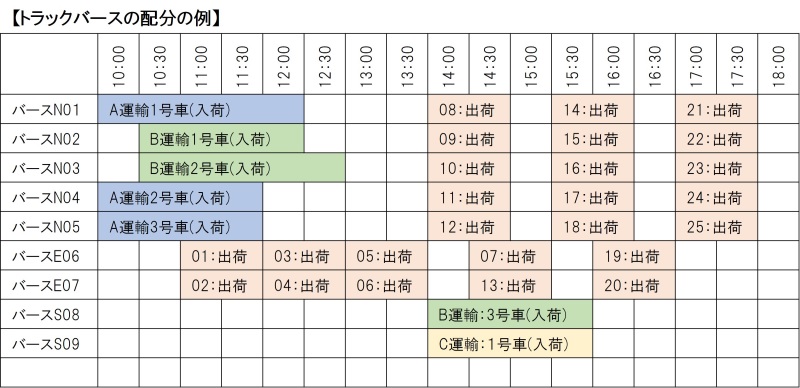
図 15:トラックバースの配分
⑥ スケジューリング結果の確認
詳細スケジューリングでは、「作業ごとの投入資源の予定」と「資源ごとの予定作業」の2種類のアウトプットが得られます。
□作業ごとの投入資源の予定
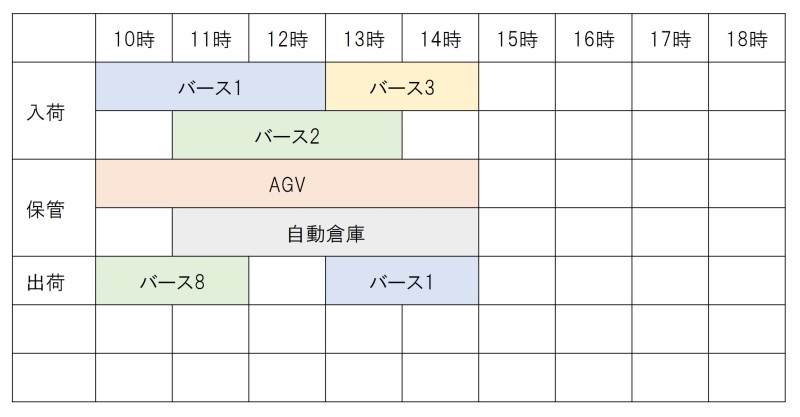
図 16:スケジューリングの結果(作業ごとの投入資源)
□資源ごとの予定作業
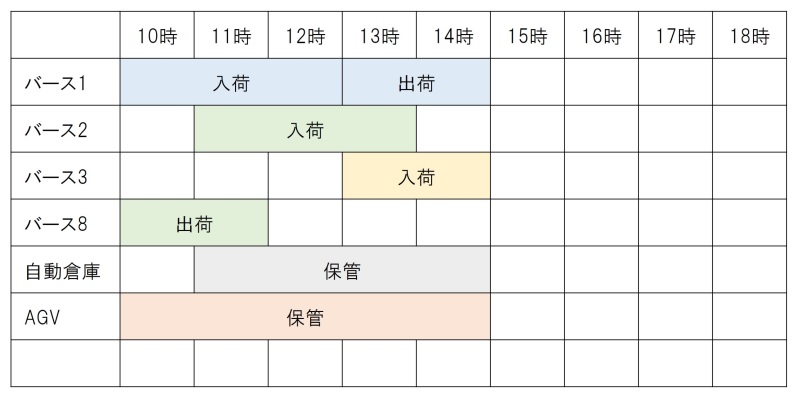
図 17::スケジューリングの結果(資源ごとの予定作業)
4) ディスパッチング
設備階層モデルのレベル2では、詳細スケジュールを、レベル1または、レベル0に対して、割り当てを行い、個々の能力や諸条件に応じた条件の制約のもと、実行されます。この機能については、ディスパッチングと称します。
ディスパッチングは、詳細スケジューリングにおいて予定されたジョブオーダ、バッチ、ロット、シフトなどを、マテハン設備や作業者へ割り当てすることで現場におけるオペレーションの流れを管理、実行します。
5)データ収集
データ収集では、マテハン設備やそれを利用した作業に関連する運転データ(実行結果)や各種パラメータを取得します。
また同時に、マテハン設備や作業進捗のリアルタイムな状態や、物流機能モデルの輸送・配送、保管、荷役、包装、流通加工などに関するデータの履歴を提供する役割も持っています。
機能階層モデルのレベル1でデータ収集の機能を持つシステムについては、分析処理が可能なようにデータ発生の都度、機能階層モデルのレベル2のアクティビティと接続して、データを集約します。
6)実行管理
実行管理では、物流機能モデルの輸送・配送、保管、荷役、包装、流通加工などのカテゴリごとに、ジョブリストにある個々の内容に従って、機能階層モデルのレベル2のアクティビティとして、レベル1または、レベル0のリソースを詳細スケジュールにもとづいてディスパッチングし、その後のデータ収集し、実行結果を得ます。
実行管理では、ロット、サブロット、バッチやシフトなど、個々の作業単位を実行したうえで、物流品質を劣化させることなく、目的地への最適ルートでの輸送が実現できるよう、倉庫内業務の最適な実行が図られます。
マテハン設備の具体的な制御については、機能階層モデルレベル1または、レベル0で定義されます。
7)トラッキング
トラッキングは、作業や装置の状態や貨物の処理状況に関する情報を提供します。
作業や装置の状態の情報には、その貨物に割り当てられた作業者、荷役に使われた梱包等資材、現在の作業進捗やアラーム情報、リワークやその他の例外事項などをリアルタイムに把握、検索できるように構築されます。
トラッキング機能を設けることにより、特定の貨物について、現時点の倉庫内における、作業進捗の状況がリアルタイムに把握することができます。
荷揃えの最終段階において、その構成品の種類や量、また、画像などによる補助情報を記録することで、効率的な検品を実行することや、検品レス出荷も可能にします。
8)設備保全
倉庫業務マネジメントが十分に機能するためには、機器の故障、破損のリスクに備え、対策を講じる必要があります。そのための設備保全は必要な機能になります。一方で、物流設計において、拠点や設備の稼働の最大化は、経営課題としての命題でもあります。
設備マネジメントの考え方により、物流設備全般(建物、建物設備、物流機器等)について、重要度検討を行ったうえで、常に最善の状態で稼働ができるよう管理することが求められます。
① 設備の重要度検討
設備の重要度判断については、『2)規定管理』で述べた、機械装置のリスト、図面、規格などにもとづいて、S・A・B・Cの4つの分類でリスク判断を行います。設備の重要度については、それぞれの企業・組織ごとに異なる基準があるが、概ね、以下条件を参考に、判断します。
Sランク:操業上絶対に運転停止できない設備(復旧まで72時間以上要する)
Aランク:入出荷が数日停止する恐れのある設備(復旧まで24~72時間程度要する)
Bランク:入出荷が一時停止する恐れのある設備(復旧まで8~24時間程度要する)
Cランク:入出荷業務停止に関係ない設備(復旧まで~8時間以内)
② 保全実行の基準
■ 事後保全(BM/Breakdown Maintenance)
装置が停止する等の現象によって、装置の故障が顕在化してから、整備、修理作業を行う保全実行の基準。実行過程において、保全終了時刻が制約となる詳細スケジューリングの制約があります。
■ 時間基準保全(TBM/Time Based Maintenance)
装置の点検、整備作業について、あらかじめ定められた周期(3か月毎、1年毎など)で作業を行う保全実行の基準。詳細スケジューリングを行う際、あらかじめ保全に要する時間を引き当てすることにより、資源(設備)能力の制約として存在します。
■ 状態基準保全(CBM/Condition Based Maintenance)
装置の点検、整備作業について、装置からの情報収集と分析結果にもとづき、一定の基準に達した時点で、整備、修理作業を行う保全実行の基準。詳細スケジューリングを行う際、あらかじめ保全に要する時間を引き当てすることにより、資源(設備)能力の制約として存在します。
■ 予知保全(PM/Predictive Maintenance)
装置の点検、整備作業について、装置からの情報収集と分析結果にもとづき、AI(人工知能)等の判断で、整備、修理作業を行う保全実行の基準。詳細スケジューリングを行う際、あらかじめ保全に要する時間を引き当てすることにより、資源(設備)能力の制約として存在します。
③ 保全計画と詳細スケジューリング
■日常点検
日常点検とは、始業前点検、運転中点検を含む、概ね1か月以内の周期で実施される検査や、部品消耗の状況確認作業のこと。
装置の点検時に必要な非稼働の時間を確保するとともに、保全資源(要員および部品)を最適なタイミングで供給する必要があります。また、非稼働の時間については、詳細スケジュ―リングの制約事項になります。
■定期点検
定期点検とは、概ね1か月以上の周期で、設備装置を停止して実施される検査や、機能回復のための部品交換や整備作業のこと。
装置の点検時に必要な非稼働の時間を確保します。非稼働の時間については、詳細スケジューリングの制約事項となります。
■整備・修理
機械装置の部品交換等による整備や、修繕作業のこと。整備、修繕作業中は、機械装置について使用できないため、あらかじめ計画されている場合は、詳細スケジューリングの制約事項となります。機械装置の使用中、または、使用開始前に発生した故障を復旧する場合は、修理復旧終了後の時刻に合わせて作業スケジュールを変更します。
④ 状態分析
機器が故障、破損する要因は、稼働時間、設置期間、設置環境の変化、不慮の事故、操作ミスなど多岐に渡ります。倉庫業務マネジメントを運用するうえで、これら、故障、破損のリスクに備える必要があり、分析に必要な情報については、機能階層モデルのレベル2(WESの領域)で情報収集し、分析します。
(状態分析に必要な収集する情報の例)
■電動機の回転数(インバーターの周波数、回転計の値)
■装置の温度(温度計の値)
■異常な音(振動計の値、騒音計の値)
■電流値(電流計の値)
■消費電力量(電力量計の値)
■設置環境(温度計の値、湿度計の値)
■装置の異常(油圧の値、圧縮空気圧の値、冷却水温度)
■その他装置そのものが外部発報する運転・停止情報や警報等
9)パフォーマンス解析
パフォーマンス解析では、不具合の修正やさらなる改善のために、倉庫業務マネジメントネジメントに関するさまざまな作業のパフォーマンスを解析します。
実際に行われたオペレーションの結果をデータ取集し、過去の履歴として築盛します。
詳細スケジューリング提供される、期待される結果と更新される実行データを比較して、パフォーマンスデータを提供します。
パフォーマンスデータとしては、資源稼働率、能力余裕、サイクルタイム、計画達成率などがあります。
<次頁を読む>第4回・WESのアクティビティと連携情報
CASE
最新導入事例
- 中部興産株式会社
- 四国牛乳輸送株式会社
- Lee Soon Seng Plastic Industries Sdn. Bhd.(LSSPI)
- SBSロジコム株式会社
- AEON MALL (CAMBODIA) LOGI PLUS CO.,LTD.
- ENEOS株式会社 川崎製油所
- TAKAIDOクールフロー株式会社
- 株式会社KITSライン
- SBSフレックネット株式会社
- 株式会社ギオン
- 株式会社秋田物流センター
- 国誉商業(上海)有限公司
- 株式会社モスフードサービス
- ヤマトロジスティクス株式会社
- スターバックス コーヒー ジャパン株式会社
- 丸善株式会社
- 株式会社ライフサポート・エガワ
- 株式会社MizkanSanmi
- 株式会社三石
- 株式会社ファミリーマート
- 株式会社花畑牧場 → 導入事例一覧へ
- サービス一覧
- 倉庫管理システム「ci.Himalayas/R2」
- クラウド型多言語版倉庫管理システム(WMS)「ci.Himalayas/GLOBAL」
- 物流KPI分析アプリ『ci.Himalayas/Compass』
- 物流向けAI-OCR Webスキャナ「@YOMU」
- 音声指示と入力で楽々作業「リスワーク」
- 音声種まき仕分け『LISSORT(リスソート)』
- 音声摘み取りピッキングシステム「ci.Superior/LISPICK」
- 庫内作業の運搬支援、運搬支援AMR(自律移動ロボット)
- 輸送品質のモニタとエビデンス管理を効率化、データロガー
- 海外ハンディソリューション「ci.Himalayas/HALO」
- 点検・検査業務を効率化・正確化・標準化、音声検査LISTEST
- クラウド型監視カメラ「GAZOCL」
- 作業映像一発検索システム「GAZOQS」
- 車番認証システム
- 人数カウントシステム
- ヒートマップ
- 属性判定システム
- 業務用インターホンシステム
- 全国どこでも簡単追跡、「カゴ車locaTor」
- 【業界別】流通小売向けソリューション
お気軽にご相談ください
お電話でのお問い合わせ
043-297-1582
受付時間 平日9:00~17:15(※土日祝除く)
メールでのお問い合わせ
資料請求・お問い合わせ当社へのアクセス
所在地 〒261-0023 千葉県千葉市美浜区中瀬 1丁目 3
建物名 幕張テクノガーデンB棟11 階
アクセス JR海浜幕張 徒歩3分 JR・京成電鉄「幕張本郷」駅よりバス13分、徒歩5分